
High frequency welding

High-Frequency welding on footwear
To praise something flawless or done with perfection, people use the word smooth. It's no wonder that at some point, the masterminds of the sneaker biz will cotton onto the idea and find a way to manufacture sans-seams sneakers. The footwear engineering fraternity discovered a way of tapping into some positive vibrations and eliminating the stitched overlaps.
The science behind the method goes back to the 1940s, when researchers worked desperately to find out how to win the war using sophisticated technology. There were many innovative theories, and a bunch of radiofrequency experiments was carried out, finding how to invest their potential for new purposes.
Of course, the ability to equip frequency and produce any microwave heat gun was the most significant concern. Still, high-frequency welding was a less damaging and potentially much more valuable invention.
Over the years, the mechanism has been streamlined, but it remains intact at heart. Molecular friction, which allows plastics to heat up and stick together, is used for high-frequency welding. Pieces that need to be joined are placed on a strong press table, and then a die is lowered on the polymers with intense pressure, a kind of welding structure, indicating the areas to be joined as a weld map.
The machine passes high-frequency waves across the material sandwiched between the table and the die, at the time when the press comes together, flapping the particles around so that they rub against each other until they get hot.

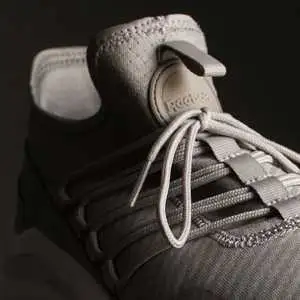
High frequecy welding on shoes tounge

High frequency welding on shoe upper
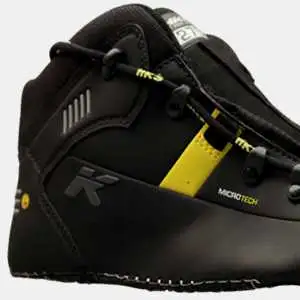
High frequency welding on sports shoe upper

Logo high frequency welding on shoe upper
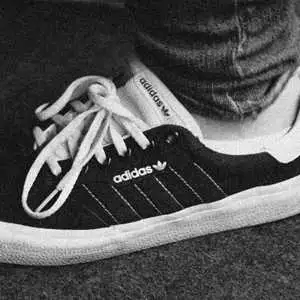
Logo high frequency welding on sneakers
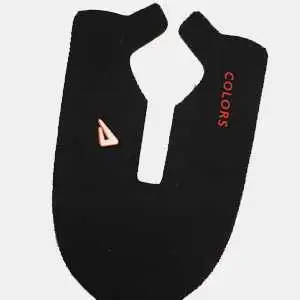
Screen printing inks
A precise and extremely powerful weld is produced by the combination of piercing heat and pressure, fusing the components until they become one. The procedure is much smoother than conventional methods of heat joining. It is suitable for high production and development for companies such as Nike (who call it Hyperfuse) or New Balance (FantomFit).
Traditionally, shoes are constructed from layers of overlapping and stitched materials; the resultant seam produces a vulnerable point that may be twice the surrounding area's width. Seams will rub on an athlete's foot and annoy it, and they are also the first component of a shoe to fall.
They are thicker than the surrounding areas as materials are joined with high-frequency welding and can also be thinner due to their compression. The invention helps shoe designers to match the characteristics of robust, rugged hiking types with the athletic footwear's lightweight performance qualities. You can see all sorts of features combining to produce a modern generation of heavy-duty sports boots. Such as the New Balance Trail buster Reengineered, Adidas Ultra Boost ATR, Nike Air Max Zero, and FILA Overpass 2.0 Fusion. Although plastics can only be welded with this high-frequency technique, there are a lot of different types that can be used. PVC and TPU sheets are the most common, but EVA and nylon can be welded, which means that a robust protective layer can be laminated over a breathable mesh.
In the sneaker world, you'll see this used a lot to protect toes and strengthen sides. There are infinite iterations of material blends out there that can include an extremely lightweight, solid, and slender piece of engineering.
Beyond the structural benefits of welded construction, a new field of visual opportunities for artists has been opened up.
The unveiling of Nike's Hyperfuse 'Olympics' pack in 2012 left people scratching their heads-the way the transparent yellow and blue overlapped to generate green added some new science to the game. Heavily layered models can now be slimmed down to produce sleek iterations of old classics, Nike's Air Max 95 SE, or other new technology, as with the Air Max 1 Flyknit mudguard.
In the future, the quest for lightweight, robust, slender, and supportive footwear will continue. There will be new ways as long as there are smart people globally, but until we can copy some unreleased Yeezy graphene rebuilds, we expect high-frequency welded uppers to be the best thing around.
Application :
High frequency sport shoes upper welding. It is suitable for PVC, PETG, APET, PETG, GAG welding plastics. Widely used for handbag making, small spraying toys, leather goods, furniture, clothing, and shoes embossing tool for plastic inflatable products, trademark, box, air tool, blanket, package bag, heat water bag, medical care objects, stationery, photo album, physical good, PVC folding box, glass box, tent, welding emblem, etc. garment and upper shoe and so on.